- Table of Contents
- Introduction
- 1. Understanding Chemical Hazards
- How to Identify Chemical Hazards
- Case Study
- 2. Proper Storage and Labeling
- Storage Best Practices
- Labeling Guidelines
- 3. Personal Protective Equipment (PPE)
- Types of PPE and Their Functions
- PPE Best Practices
- 4. Safe Handling and Usage
- Handling Guidelines
- Common Mistakes to Avoid
- 5. Ventilation and Engineering Controls
- 6. Emergency Preparedness and Response
- 7. Disposal and Environmental Considerations
- Safe Disposal Methods
- Sustainability Tips
- Conclusion
Introduction
Chemicals play a crucial role in industries such as healthcare, manufacturing, and research. While they are essential, improper handling can lead to serious health risks, environmental damage, and even fatalities. According to the International Labour Organization (ILO), hazardous substances contribute to over 1 million deaths annually worldwide. Furthermore, the Occupational Safety and Health Administration (OSHA) reports that over 190,000 illnesses and 50,000 deaths each year in the United States alone are linked to hazardous chemical exposure.
Ensuring the safe handling, storage, and disposal of chemicals is vital to prevent accidents, injuries, and long-term health issues. This article provides detailed guidelines on best practices for handling chemicals safely, minimizing risks, and complying with safety regulations.
1. Understanding Chemical Hazards
Understanding the inherent dangers of chemicals is fundamental to effective risk management. Chemicals come in various forms and can be classified based on their hazards:
Type of Hazard | Description | Examples |
---|---|---|
Toxic | Harmful when inhaled, swallowed, or absorbed into the skin. Long-term exposure can cause chronic diseases. | Pesticides, mercury, lead |
Corrosive | Destroys or damages living tissues on contact. Can cause severe burns and eye damage. | Sulfuric acid, sodium hydroxide |
Flammable | Easily ignites when exposed to heat, sparks, or flames. Some can form explosive vapors. | Ethanol, acetone, gasoline |
Reactive | Unstable substances that may explode or release toxic gases when mixed with other chemicals. | Hydrogen peroxide, sodium metal |
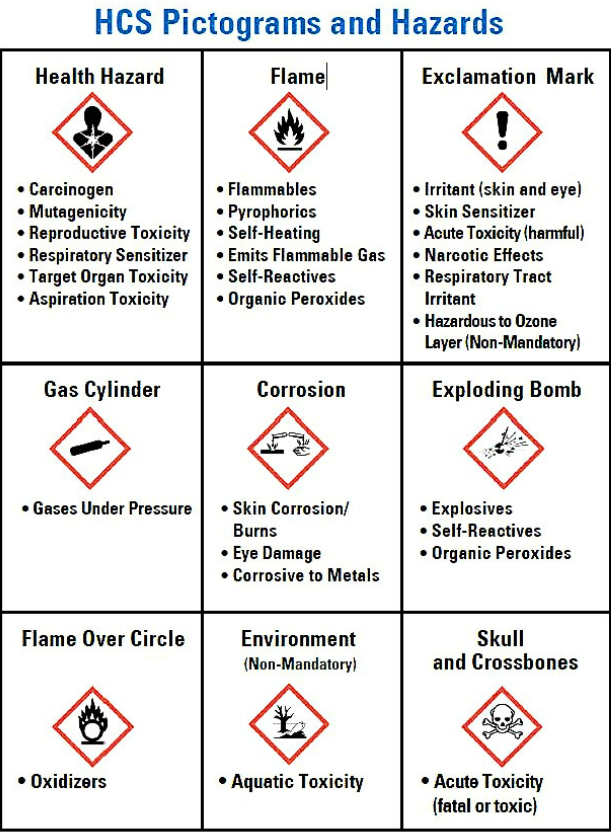
The consequences of mishandling chemicals extend to both human health and the environment. Long-term exposure to hazardous substances can lead to chronic conditions such as respiratory diseases or skin disorders. Furthermore, improper disposal of chemicals can cause damage on ecosystems, polluting water sources, harming wildlife, and degrading soil quality. To mitigate these risks, workers must familiarize themselves with Safety Data Sheets (SDS). These sheets provide comprehensive information about a chemical, including its properties, potential hazards, and guidelines for safe handling and emergency response. By routinely reviewing SDS documents, individuals can take informed precautions and respond effectively to potential dangers.
How to Identify Chemical Hazards
- Read Safety Data Sheets (SDS) provided by manufacturers for detailed hazard information.
- Look for hazard symbols on chemical labels, such as the Globally Harmonized System (GHS) pictograms.
- Use online resources like the NIOSH Pocket Guide to Chemical Hazards for additional safety guidance.
Case Study
A 2019 study by the National Institute for Occupational Safety and Health (NIOSH) found that 30% of workplace chemical accidents occurred due to a lack of hazard identification. Facilities that implemented rigorous chemical safety training saw a 45% reduction in accidents over five years.
2. Proper Storage and Labeling
Storing and labeling chemicals correctly is a cornerstone of safety in any environment that handles hazardous substances. To prevent accidents, chemicals must be stored in appropriate, clearly labeled containers designed to resist corrosion or leaks. Segregating chemicals by their hazard class is another vital step. For instance, acids and bases should be stored separately to avoid reactions. Maintaining stable environmental conditions, such as temperature and humidity, further reduces risks of unintentional reactions or degradation.
Storage Best Practices
Aspect | Best Practice |
---|---|
Segregation | Store chemicals by compatibility groups (e.g., acids separate from bases/oxidizers). |
Fire Safety | Use fire-resistant cabinets for flammable substances. |
Stock Management | Avoid overstocking to reduce risk of spills and clutter. |
Sealing | Ensure all containers are properly sealed to prevent evaporation and contamination. |
Routine Checks | Regularly check storage areas for leaks, corrosion, or expired chemicals. |
Temperature | Maintain stable temperatures to prevent chemical reactions. |
Ventilation | Use exhaust systems to remove harmful vapors and ensure proper airflow. |
Containment | Use secondary containment trays to enhance safety. |
Labeling chemicals accurately is equally important. Labels should include the chemical name, associated hazards, and appropriate precautionary measures. Clear signage in storage areas can enhance awareness, guiding employees to handle substances carefully. Chemical compatibility is a critical aspect to consider during storage. Storing incompatible substances together, such as oxidizers with flammables, can trigger dangerous reactions. For example, a study by OSHArevealed that nearly 30% of chemical-related incidents arise from improper storage practices.
Labeling Guidelines
- Use GHS-compliant labels that include chemical names, hazard symbols, and safety precautions.
- Ensure labels are water-resistant and remain intact over time.
- If transferring chemicals into new containers, ensure they are labeled immediately.
3. Personal Protective Equipment (PPE)
Personal Protective Equipment (PPE) serves as the first barrier between workers and hazardous chemicals. PPE includes a range of protective items such as gloves, goggles, respirators, and full-body suits. Gloves protect hands from chemical burns or irritants, while goggles safeguard eyes from splashes or fumes. Respirators are essential when handling volatile chemicals that emit harmful vapors.
Choosing the right PPE requires an understanding of the chemical in question. For instance, rubber gloves are ideal for acids, while nitrile gloves may be more suitable for solvents. Proper maintenance of PPE ensures its effectiveness—this includes regular inspections for damage and cleaning after use. Neglecting PPE can lead to compromised safety, as evidenced by statistics from the National Safety Council, which found that improper or inadequate use of PPE contributes to 25% of chemical-related workplace injuries.
Types of PPE and Their Functions
Type of PPE | Function | Example Chemicals |
---|---|---|
Gloves | Prevents skin absorption of harmful chemicals | Acids, solvents |
Goggles | Shields eyes from splashes and vapors | Chlorine, ammonia |
Respirators | Protects against inhalation of toxic fumes | Formaldehyde, benzene |
Lab Coats & Aprons | Prevents chemical spills from reaching the skin | Hydrochloric acid, bleach |
PPE Best Practices
- Choose gloves resistant to the specific chemical being handled (e.g., nitrile gloves for solvents, butyl gloves for ketones).
- Replace PPE regularly to prevent contamination.
- Ensure proper fit to maximize protection.
A 2022 study by OSHA found that 60% of chemical-related injuries resulted from inadequate PPE. Companies that enforced PPE compliance reduced their injury rates by 70%.
4. Safe Handling and Usage
Safe chemical handling is not just about wearing PPE; it requires thorough preparation and adherence to standardized procedures. Workers should assess risks before beginning any task, ensuring they are aware of potential hazards and are equipped with the necessary tools and protective gear. Following step-by-step procedures can prevent common errors, such as spills, contamination, or unintended chemical reactions.
One prevalent mistake is mixing incompatible chemicals without understanding their properties. For example, mixing bleach with ammonia releases toxic chloramine gas, which can cause severe respiratory distress. Another common oversight is neglecting ventilation requirements. Without adequate airflow, toxic fumes can accumulate, posing health risks. Studies demonstrate that proper ventilation systems can reduce chemical exposure by up to 60%. Tools such as funnels, enclosed systems, and automated transfer devices further minimize risks during chemical transfer or mixing operations.
Handling Guidelines
- Always work in well-ventilated areas to avoid inhaling harmful fumes.
- Use mechanical transfer devices instead of manually pouring hazardous liquids.
- Never mix chemicals unless explicitly instructed—unexpected reactions can be deadly.
- Follow standard operating procedures (SOPs) for handling specific chemicals.
Common Mistakes to Avoid
- Ignoring SDS recommendations before using a new chemical.
- Using inappropriate storage containers, which can cause leaks.
- Failing to clean up minor spills immediately, leading to contamination.
5. Ventilation and Engineering Controls
Ventilation and engineering controls are critical components of chemical safety. Fume hoods, for example, play a pivotal role by capturing hazardous vapors and preventing them from spreading into the workplace. Laboratories and industries must ensure that their ventilation systems are functional and meet regulatory standards. Routine testing and maintenance of these systems are necessary to maintain airflow and prevent malfunctions.
Containment strategies are another effective method for minimizing exposure. Using enclosed systems for highly volatile or reactive chemicals reduces the likelihood of accidental release. Workplaces can implement simple measures, such as ensuring laboratory doors remain closed during operations, to enhance containment. The Environmental Protection Agency (EPA) reports that effective ventilation and engineering controls can mitigate 90% of workplace chemical exposure risks.
Control Type | Purpose |
---|---|
Fume Hoods | Capture and remove hazardous vapors |
Airflow Testing | Ensure adequate ventilation |
6. Emergency Preparedness and Response
Even with preventive measures, emergencies can still occur. Being prepared for incidents such as chemical spills, fires, or exposure is vital to minimizing harm. First aid protocols should be well-known to all employees. For example, in the event of skin contact, the affected area should be rinsed with water for at least 15 minutes. If a chemical is inhaled, the individual should move to fresh air immediately.
Spill kits are invaluable for managing minor incidents. They typically include absorbent materials, neutralizers, and protective equipment. Proper training ensures employees know how to use these kits effectively. For fires involving flammable chemicals, workplaces must have accessible fire extinguishers and train staff in their use.
Emergency Protocols | Details |
---|---|
Spill Kits | Keep absorbents and neutralizers on hand. |
First Aid | Know emergency response steps for exposure. |
Skin Contact | Rinse thoroughly for at least 15 minutes. |
Eye Exposure | Flush eyes immediately with water. |
Inhalation | Seek fresh air and medical attention if needed. |
7. Disposal and Environmental Considerations
The final stage of chemical management—disposal—is often overlooked but is critically important. Improper disposal can lead to environmental contamination and legal penalties. Hazardous chemicals must be disposed of in accordance with local and international regulations. Certified facilities equipped for incineration or chemical treatment are essential for safely disposing of toxic substances.
Sustainability is an emerging focus in chemical safety. Reducing chemical use and substituting hazardous chemicals with safer alternatives are steps toward a greener future. In a recent study, organizations adopting sustainable practices reported a 20% decrease in chemical waste, highlighting the effectiveness of these strategies.
Safe Disposal Methods
Chemical Type | Disposal Method |
---|---|
Flammable solvents | Incineration |
Acids and bases | Neutralization |
Heavy metals | Hazardous waste treatment |
Sustainability Tips
- Reduce chemical waste by purchasing only what’s needed.
- Recycle solvents when possible.
- Adhere to local and international waste disposal regulations.
Conclusion
Handling chemicals safely is a shared responsibility that requires vigilance, education, and proactive measures. By understanding hazards, implementing safety protocols, and embracing sustainable practices, individuals and organizations can significantly reduce risks.
To stay updated on chemical safety, subscribe to our newsletter or enroll in our workplace safety courses. Safety begins with awareness—take action today!