- Table of Contents
- Introduction
- What Is Six Sigma?
- Why Is Six Sigma Important?
- Improved Quality
- Enhanced Efficiency
- Data-Driven Decision Making
- Customer Focus
- Continuous Improvement
- Exploring Six Sigma Belt Levels
- How Much Does Six Sigma Cost?
- Training Costs
- Resource Investments
- Project Costs
- Opportunity Costs
- Consulting and Support Costs
- Certification and Recognition Costs
- Implementing Six Sigma: A Step-by-Step Guide
- Step #1: Leadership Commitment
- Step #2: Training and Certification
- Step #3: Project Selection
- Step #4: DMAIC Methodology
- Step #5: Data Collection and Analysis
- Step #6: Process Improvement
- Step #7: Control and Sustaining Improvements
- Step #8: Continuous Learning and Adaptation
- Exploring Six Sigma Across Industries
- Healthcare:
- Manufacturing:
- Service Sector:
- Telecommunications:
- Education:
- Retail:
- The Future of Six Sigma
- Emerging Technologies and Six Sigma
- Automation and Streamlined Processes
- Data Analytics and Big Data
- IoT (Internet of Things) and Six Sigma
- Advanced Visualisation Tools
- Blockchain and Quality Assurance
- Augmented Reality (AR) and Virtual Reality (VR)
- Sustainability and Environmental Considerations
- Conclusion
Introduction
In a world where organisations strive for continuous improvement and excellence, the concept of the Six Sigma Belt emerges as a powerful tool for driving efficiency and ensuring top-notch quality. With its origins rooted in statistical analysis and process optimisation, Six Sigma has become synonymous with process excellence and has revolutionised industries worldwide. In this blog post, we will embark on a journey to understand the fundamentals of Six Sigma, explore the significance of the Six Sigma Belt, delve into its impact on operational performance, and equip you with practical knowledge to implement Six Sigma in your company. So, fasten your seatbelts and get ready to explore the realm of the Six Sigma Belt and its transformative potential.
What Is Six Sigma?
Six Sigma is a disciplined approach to process improvement that minimises variations and defects in a company's processes. Motorola originally developed it in the 1980s and later popularised by companies like General Electric. The term "Six Sigma" refers to a statistical measure that represents a high level of process capability. Six Sigma aims to achieve near-perfect performance by reducing process variations and defects to an extremely low level.
Why Is Six Sigma Important?
One might wonder what makes Six Sigma such a crucial methodology in today's business landscape. Advocates of Six Sigma assert that its strategic advantages encompass a remarkable 50% reduction in process costs, improved cycle times, reduced material wastage, enhanced comprehension of customer needs, elevated customer satisfaction and value, and the delivery of more dependable products and services, according to TechTarget. That being said, let's discuss some of the benefits as mentioned earlier, as well as other advantages of implementing Six Sigma:
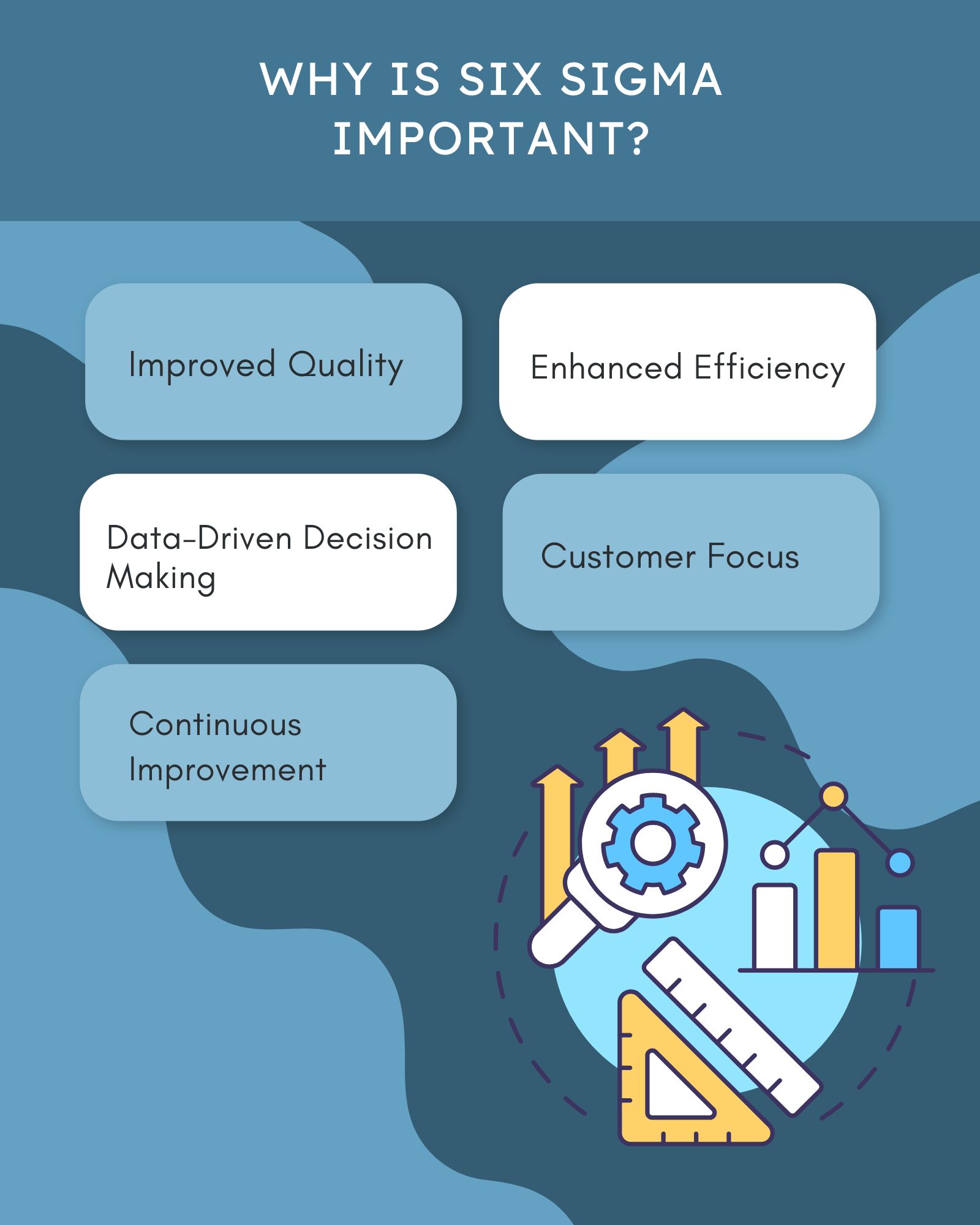
Improved Quality
Six Sigma's primary objective is to enhance the quality of products or services by identifying and eliminating defects. Providing high-quality, error-free products and services is paramount in an era of soaring customer expectations. By reducing variations and defects to an exceptionally low level, Six Sigma ensures that each product or service consistently meets or exceeds customer expectations. This improved quality leads to higher customer satisfaction and fosters brand loyalty.
Enhanced Efficiency
Efficiency is the backbone of any successful organisation. Six Sigma achieves efficiency by streamlining processes and minimising waste. Inefficiencies, redundancies, and bottlenecks are identified and eliminated, ensuring that resources are utilised optimally. By optimising resource allocation, organisations can improve productivity, reduce operational costs, and enhance overall efficiency. This streamlined approach not only boosts the bottom line but also creates a more agile and responsive organisation.
Data-Driven Decision Making
In the age of information, data-driven decision-making is essential for sustainable growth. Six Sigma relies heavily on robust data analysis and measurement techniques. Organisations gain valuable insights into their processes by collecting and analysing relevant data. This data-driven approach enables informed decision-making, as managers and leaders can rely on objective evidence rather than intuition or guesswork. Informed decisions are more accurate, leading to the implementation of effective solutions and strategies.
Customer Focus
Customer satisfaction is the cornerstone of any successful business. Six Sigma strongly emphasises understanding customer requirements and aligning processes to meet those needs. Organisations can gain a competitive edge in the market by identifying and addressing customer pain points. Customer-centric processes attract new customers and retain existing ones, leading to increased revenue and market share. Understanding customer needs also allows organisations to anticipate future demands, enabling them to stay ahead of the competition.
Continuous Improvement
The business landscape is dynamic, with new challenges and opportunities arising constantly. Six Sigma promotes a culture of continuous improvement through methodologies like DMAIC (Define, Measure, Analyse, Improve, Control). This structured approach ensures that organisations do not become complacent after achieving initial improvements. Instead, it encourages them to continually assess their processes, identify areas for enhancement, and implement strategic changes. Continuous improvement is not just a one-time effort; it becomes ingrained in the organisational culture, leading to sustained excellence over time.
In summary, Six Sigma's immense importance lies in its holistic approach to organisational enhancement. Six Sigma equips organisations with the tools they need to thrive in a competitive environment by addressing quality, efficiency, data-driven decision-making, customer focus, and continuous improvement. Its principles empower businesses to adapt to changing market demands, enhance customer experiences, and achieve long-term success. By systematically implementing Six Sigma methodologies, organisations can position themselves as leaders in their respective industries, driving innovation, growth, and customer satisfaction.
Exploring Six Sigma Belt Levels
A unique aspect of Six Sigma is its Belt system, indicating different levels of expertise and roles within the methodology. The table below illustrates the various Six Sigma Belt levels and their respective responsibilities:
Belt Level | Responsibilities |
Yellow Belt | Participate in improvement projects, support Green and Black Belts |
Green Belt | Lead small-scale improvement projects, assist Black Belts |
Black Belt | Lead complex projects, mentor Green Belts, and assist in strategic decision-making |
Master Black Belt | Provide training, mentorship, and strategic guidance to Black Belts and Green Belts |
Table 1: Six Sigma Belt Levels and Their Respective Responsibilities
How Much Does Six Sigma Cost?
Implementing Six Sigma is a strategic investment that promises substantial returns through improved efficiency, enhanced quality, and increased customer satisfaction. However, weighing the costs associated with Six Sigma implementation against the benefits it offers is essential. Let's explore the various cost considerations involved in implementing Six Sigma:
Training Costs
One of the significant expenses in Six Sigma implementation is training. Organisations need to invest in training programmes for employees at different levels, ranging from Yellow Belt to Master Black Belt. The cost of these programmes varies depending on the depth and duration of the training. Online courses might be more cost-effective, while in-person training sessions led by certified professionals tend to be more comprehensive but come at a higher price. Despite the initial investment, well-trained Six Sigma professionals are essential assets who can drive impactful improvements within the organisation. And guess what? You’ve come to the right place to do just that. Get in touch with us now for more information about our courses.
Resource Investments
Implementing Six Sigma may require investments in various resources, including software tools, data analysis capabilities, and project management systems. These tools are vital for collecting, analysing, and interpreting data accurately. The choice of resources depends on the organisation's specific requirements and the complexity of the projects undertaken. While these resources come with a price tag, they are essential for ensuring the successful execution of Six Sigma projects.
Project Costs
Six Sigma projects themselves may incur costs related to process redesign, data collection and analysis, and improving initiatives. The complexity and scope of the projects determine these costs. For instance, a large-scale process redesign involving multiple departments may require significant financial resources, while smaller projects focused on a specific area might incur comparatively lower costs. Organisations must conduct a cost-benefit analysis to assess each project's potential return on investment (ROI).
Opportunity Costs
Implementing Six Sigma requires significant time and effort from employees and management. The time spent on Six Sigma initiatives might not be spent on other projects or tasks. These opportunity costs must be considered when evaluating the overall investment in Six Sigma. However, the benefits derived from improved processes, customer satisfaction, and competitive advantage often outweigh these opportunity costs in the long run.
Consulting and Support Costs
Some organisations opt to hire external consultants or Six Sigma experts to guide them through the implementation process. These experts provide valuable insights, knowledge, and best practices, accelerating the implementation timeline and ensuring the effectiveness of Six Sigma initiatives. While hiring consultants incurs additional costs, their expertise can significantly enhance the success of Six Sigma projects.
Certification and Recognition Costs
Organisations often seek certification from relevant Six Sigma bodies to validate their commitment to quality and process improvement. Achieving certification involves costs related to examinations, audits, and documentation. While certification is not mandatory, but it can enhance the organisation's reputation, increasing credibility and potential business opportunities.
Organisations must budget carefully and plan strategically when embarking on a Six Sigma implementation journey. While costs are involved, the potential benefits, including improved efficiency, reduced operational costs, and increased customer satisfaction, far outweigh the initial investment. Moreover, the culture of continuous improvement fostered by Six Sigma ensures that the organisation continues to evolve, adapting to changing market demands and staying ahead of the competition. Through meticulous planning, organisations can harness the transformative power of Six Sigma while managing costs effectively, ensuring a positive impact on both the bottom line and overall operational excellence.
Implementing Six Sigma: A Step-by-Step Guide
Implementing Six Sigma effectively requires a systematic approach and the active involvement of employees at all levels of the organisation. Here's a comprehensive step-by-step guide to help organisations successfully integrate Six Sigma into their operations:
Step #1: Leadership Commitment
The first and foremost step in implementing Six Sigma is securing commitment from top leadership. Without the active support of executives and managers, it's challenging to drive change throughout the organisation. Leaders need to champion the initiative, allocate necessary resources, and set the tone for a culture of continuous improvement. Their visible commitment sends a strong message to the entire workforce, emphasising the importance of Six Sigma in achieving organisational goals.
Step #2: Training and Certification
It is crucial to identify individuals who will lead Six Sigma projects and provide them with appropriate training. Employees can undergo training at different levels, such as Yellow Belt, Green Belt, or Black Belt, based on their roles and responsibilities within the projects. Certification programmes equip individuals with the skills and knowledge to effectively execute improvement initiatives. Continuous training ensures that employees stay up-to-date with the latest methodologies and tools, enhancing their problem-solving capabilities.
Step #3: Project Selection
Careful project selection is vital to the success of Six Sigma initiatives. Projects should align with organisational goals, focusing on areas critical to business objectives and customer satisfaction. Tools like project charters and stakeholder analysis can aid in defining project goals, scope, and success criteria. Prioritising projects based on their potential impact and feasibility ensures that resources are allocated to initiatives that deliver the most significant value to the organisation.
Step #4: DMAIC Methodology
DMAIC (Define, Measure, Analyse, Improve, Control) is the foundation for Six Sigma projects. This structured problem-solving approach provides a clear framework for project execution.
Define: Clearly define the problem, project goals, scope, and stakeholders involved.
Measure: Gather relevant data to understand the current process performance. Establish baseline metrics to measure progress.
Analyse: Use statistical tools and techniques to identify the root causes of defects or variations. Analyse the data to gain insights into process inefficiencies.
Improve: Develop and implement improvement strategies based on data analysis. Implement solutions using tools like process mapping, root cause analysis, and hypothesis testing.
Control: Establish control mechanisms to monitor the performance of improved processes. Implement process controls, standard operating procedures, and measurement systems to sustain continuous improvements.
Step #5: Data Collection and Analysis
Collecting relevant data is the cornerstone of Six Sigma. Accurate data helps understand the process's current state and identify improvement areas. Statistical tools and techniques, such as control charts, regression analysis, and hypothesis testing, are used to analyse the data. Through data analysis, organisations can identify patterns, trends, and correlations, enabling them to make informed decisions and identify the root causes of process issues.
Step #6: Process Improvement
Improvement strategies are developed and implemented based on the insights gained from data analysis. Process mapping helps visualise the current state of processes, highlighting inefficiencies and bottlenecks. Root cause analysis helps identify the underlying causes of defects or variations. Hypothesis testing validates proposed solutions. Organisations can optimise processes, reduce defects, and enhance overall efficiency by systematically addressing these issues.
Step #7: Control and Sustaining Improvements
Implementing solutions is not the end of the Six Sigma journey; it's the beginning of sustained improvement. Establishing control mechanisms ensures that the improved processes continue to perform at the desired level. This involves implementing process controls, standard operating procedures, and ongoing measurement systems. Regular monitoring and measurement are essential to track process performance. If deviations occur, corrective actions can be taken promptly to maintain the gains achieved through Six Sigma initiatives.
Step #8: Continuous Learning and Adaptation
Six Sigma is not a one-time effort but a continuous journey. Organisations should encourage a culture of continuous learning and adaptation. Conducting regular reviews of implemented projects, analysing results, and identifying lessons learned help refine future initiatives. Feedback loops, both internal and external, facilitate ongoing improvement. Organisations can stay ahead of the competition by continuously adapting to changing market demands and evolving technologies and ensuring long-term success.
By following this step-by-step guide, organisations can harness the full potential of Six Sigma, driving improvements in quality, efficiency, and customer satisfaction. The structured approach provided by Six Sigma methodologies empowers organisations to tackle complex challenges systematically, fostering a culture of continuous improvement and ensuring sustainable growth in today's competitive business landscape.
Exploring Six Sigma Across Industries
Six Sigma is a versatile methodology that transcends industry boundaries, offering its principles and techniques to diverse sectors. Its systematic approach to process improvement and quality management has found applications in various industries, revolutionising operations and enhancing customer satisfaction. Let's explore how Six Sigma has made a significant impact in different sectors:
Healthcare
In the healthcare industry, the stakes are high, and errors can have life-altering consequences. Six Sigma methodologies have been instrumental in improving patient care, enhancing operational efficiency, and optimising hospital processes. By minimising errors and streamlining workflows, healthcare providers can offer better services to patients. Six Sigma tools help identify inefficiencies, reduce waiting times, and enhance the overall patient experience. Moreover, it aids in reducing medical errors, ensuring accurate diagnoses, and improving the quality of healthcare services, ultimately saving lives and improving public health outcomes.
Manufacturing
In manufacturing, Six Sigma is synonymous with quality control. Manufacturers can ensure product reliability and customer satisfaction by identifying and eliminating defects. Six Sigma techniques are applied in areas like production lines, supply chain management, and quality assurance processes. Statistical process control (SPC) methods are used to monitor production processes, ensuring consistency and minimising variations. By optimising manufacturing processes, Six Sigma helps reduce waste, improve yield rates, and ultimately lead to cost savings and increased competitiveness in the market.
Service Sector
The service industry, encompassing banking, hospitality, insurance, and IT sectors, has embraced Six Sigma to enhance customer experiences. By streamlining service delivery processes, organisations can reduce service time, improve accuracy, and increase customer satisfaction. Six Sigma techniques are used in the banking sector to optimise transaction processes, leading to quicker and error-free banking services. In hospitality, it helps to improve guest experiences, from booking procedures to check-out processes. Implementing Six Sigma principles in the service sector enhances customer loyalty, positive word-of-mouth, and improved brand reputation.
Telecommunications
The telecommunications industry relies heavily on efficient processes to handle vast amounts of data and ensure seamless communication services. Six Sigma methodologies are employed to optimise network performance, reduce downtime, and improve customer service. By identifying and resolving issues related to call drops, network congestion, and service outages, telecommunication companies can enhance the reliability of their services. Six Sigma tools like root cause analysis and failure mode effects analysis (FMEA) are utilised to proactively address potential problems, ensuring uninterrupted communication services for customers.
Industry | Six Sigma Application |
Healthcare | Optimising hospital processes, improving patient care |
Manufacturing | Quality control, process optimisation, reducing defects |
Service Sector | Streamlining service delivery, enhancing customer experiences |
Telecommunications | Network optimisation, reducing downtime, improving services |
Education | Improving administrative processes, enhancing teaching methods |
Table 2: Applications of Six Sigma across industries
Education
Six Sigma has been used in the education sector to improve administrative processes, student enrollment, and academic outcomes. By optimising administrative workflows, educational institutions can reduce paperwork, enhance efficiency, and improve the overall quality of services. Six Sigma techniques are also applied to analyse and improve teaching methodologies, ensuring students receive high-quality education. By focusing on student performance metrics and identifying areas for improvement, educational institutions can enhance the learning experience and contribute to the academic success of their students.
Retail
Retailers face numerous challenges, including inventory management, supply chain optimisation, and customer satisfaction. Six Sigma principles are applied to optimise inventory levels, reduce stockouts, and enhance demand forecasting accuracy. By analysing customer preferences and purchasing patterns, retailers can tailor their offerings, leading to increased customer satisfaction and loyalty. Additionally, Six Sigma techniques aid in improving the efficiency of supply chain processes, ensuring timely deliveries and reducing lead times. This results in cost savings, improved customer experiences, and a competitive edge in the retail market.
In summary, Six Sigma's applicability across diverse industries underscores its versatility and effectiveness as a problem-solving methodology. By embracing Six Sigma principles and tools, organisations in various sectors can drive continuous improvement, enhance operational efficiency, and deliver exceptional value to their customers. The widespread adoption of Six Sigma across industries demonstrates its universal appeal and its positive impact on organisations' performance, making it a valuable asset in the pursuit of excellence and customer satisfaction.
The Future of Six Sigma
As we look ahead, the future of Six Sigma is inseparable from the rapid advancements in technology and the constant quest for innovation. The integration of technology and innovation not only enhances the capabilities of Six Sigma but also enables organisations to achieve greater efficiency, accuracy, and competitiveness. Let's explore how Six Sigma is evolving in the face of these changes:
Emerging Technologies and Six Sigma
Six Sigma is embracing emerging technologies that are redefining the landscape of process improvement and data analysis. Artificial intelligence (AI) and machine learning (ML) are being incorporated into Six Sigma methodologies. These technologies enable predictive analytics, allowing organisations to identify potential issues before they occur. For instance, predictive maintenance powered by AI can predict equipment failures, leading to reduced downtime and cost savings.
Automation and Streamlined Processes
Automation is a pivotal aspect of the future of Six Sigma. Automation technologies, including robotic process automation (RPA), are being used to streamline processes, reduce human error, and enhance overall efficiency. Organisations can redirect human resources to more critical decision-making processes by automating routine and repetitive tasks, accelerating project timelines and reducing operational costs.
Data Analytics and Big Data
The influx of big data and the advancement of data analytics tools have enriched Six Sigma's problem-solving capabilities. Organisations leverage data from various sources to gain deeper insights into their processes. Big data analytics allows for identifying complex patterns, trends, and correlations that were previously challenging to detect. The integration of Six Sigma with big data analytics equips organisations to make data-driven decisions with greater precision.
IoT (Internet of Things) and Six Sigma
IoT devices are becoming increasingly prevalent in various industries. The data collected from these devices can be analysed using Six Sigma methodologies to identify process inefficiencies and predict future issues. For example, IoT sensors can provide real-time data on equipment performance and product quality in manufacturing, enabling proactive quality control measures.
Advanced Visualisation Tools
Visualisation tools, including advanced dashboards and real-time reporting systems, are being integrated into Six Sigma processes. These tools enable organisations to monitor project progress, identify bottlenecks, and visualise data in a comprehensible manner. They offer stakeholders and project teams a clear view of project status, making it easier to make informed decisions and take timely actions.
Blockchain and Quality Assurance
Blockchain technology is being explored to enhance quality assurance processes. It provides a secure and transparent way to track and verify the quality of products or services throughout the supply chain. By utilising blockchain, organisations can ensure that product quality is maintained from the source to the end customer, reducing the risk of counterfeiting and fraud.
Augmented Reality (AR) and Virtual Reality (VR)
AR and VR technologies are being integrated with Six Sigma in training and problem-solving. They provide immersive training environments for Six Sigma practitioners, allowing them to practise problem-solving scenarios and simulations in a risk-free setting. These technologies enhance the training experience and help individuals grasp complex concepts more effectively.
Sustainability and Environmental Considerations
As the world becomes more focused on sustainability and environmental responsibility, Six Sigma is adapting to address these concerns. Organisations are incorporating Six Sigma methodologies to reduce waste, conserve resources, and minimise carbon footprint. By optimising processes for sustainability, organisations not only reduce their impact on the environment but also cut costs and enhance their reputation.
In short, the future of Six Sigma is characterised by its seamless integration with cutting-edge technology and innovative practices. The utilisation of emerging technologies, automation, big data analytics, IoT, visualisation tools, and other advancements amplifies the power of Six Sigma in driving continuous improvement, enhancing quality, and maintaining a competitive edge. By embracing these trends, organisations can position themselves for sustained success in an ever-evolving business landscape, achieving not only operational excellence but also contributing to the greater good through sustainable and responsible practices.
Conclusion
Six Sigma, focusing on reducing defects and process variations, is a powerful methodology that can drive significant improvements in quality, efficiency, and customer satisfaction. The concept of Six Sigma Belt, with its various levels of expertise, empowers individuals to lead improvement initiatives and implement the principles of Six Sigma effectively. By investing in Six Sigma and embracing a culture of continuous improvement, companies can position themselves for long-term success in today's competitive marketplace.
Intrigued by Six Sigma's transformative potential? Our course, Six Sigma Uses & Implementation, unlocks the secrets to mastering this powerful methodology. Empower your team to revolutionise your processes, enhance efficiency, and exceed customer expectations, paving the way for unparalleled success in the business arena. Don't just thrive; lead the way with Six Sigma expertise! Enrol now or contact us for more information.