- Table of Contents
- Introduction
- 1. Lean Six Sigma Green Belt Training (Coursera)
- 2. Operational Excellence for Leaders (MIT Sloan Executive Education)
- 3. Kaisen Practitioner Certification (Kaisen Institute)
- 4. Total Productive Maintenance (TPM) Certification (Udemy)
- 5. Business Process Management (BPM) Certification (edX)
- 6. Operational Excellence in Manufacturing (LinkedIn Learning)
- 7. Continuous Improvement: Tools and Techniques (Skillshare)
- 8. Developing Operational Excellence In The Process Industry (Holistique Training)
Introduction
Operational excellence is a systematic approach to achieving superior organisational performance and efficiency. It involves continuous process improvement, minimising waste, and maximising value creation. By adopting best practices, leveraging advanced methodologies like Lean and Six Sigma, and fostering a culture of continuous improvement, organisations can enhance productivity, reduce costs, and deliver higher-quality products and services. Operational excellence aims to create a sustainable competitive advantage by ensuring all operations aspects align with the organisation's strategic goals.
1. Lean Six Sigma Green Belt Training (Coursera)
- Summary: This course focuses on the Lean Six Sigma methodology, combining lean manufacturing principles with Six Sigma quality control techniques to improve processes, reduce waste, and enhance quality.
- Duration: 4 weeks
- Language: English
- Level: Intermediate
What does a Lean Six Sigma Green Belt Training Course teach you?
- The DMAIC (Define, Measure, Analyse, Improve, Control) methodology.
- Data analysis, process improvement techniques, and project management skills.
- Identifying and eliminating waste, reducing variation, and improving efficiency.
Who should take Lean Six Sigma Green Belt Training course?
- Professionals in manufacturing, quality control, operations, and process improvement roles.
- Individuals seeking to enhance their problem-solving and project management skills.
- Those aspiring to become Six Sigma project leaders or team members.
Why should take Lean Six Sigma Green Belt Training course?
- To gain valuable skills in process improvement and quality management.
- To increase career opportunities and earning potential in various industries.
- To contribute to organisational efficiency and effectiveness by leading improvement projects.
2. Operational Excellence for Leaders (MIT Sloan Executive Education)
- Summary: This course is designed for leaders and managers to understand and implement operational excellence principles within their organisations. It focuses on leadership strategies, performance management, and continuous improvement.
- Duration: 1 week
- Language: English
- Level: Advanced
What does an Operational Excellence for Leaders Course teach you?
- Leadership principles, performance metrics, and change management.
- Strategies for driving operational excellence and fostering a culture of continuous improvement.
- Aligning organisational goals with operational processes.
Who should take Operational Excellence for Leaders course?
- Senior managers, executives, and leaders responsible for operational performance.
- Professionals aiming to implement operational excellence initiatives within their organisations.
- Individuals seeking to enhance their leadership and strategic planning skills.
Why should take Operational Excellence for Leaders course?
- To develop a strategic approach to operational excellence and performance management.
- To improve leadership capabilities and drive organisational success.
- To foster a culture of continuous improvement and innovation within the organisation.
3. Kaizen Practitioner Certification (Kaizen Institute)
- Summary: This course focuses on the Kaizen philosophy of continuous improvement. Participants learn practical tools and techniques to implement Kaizen initiatives in their workplaces.
- Duration: 1-2 weeks
- Language: English
- Level: Intermediate
What does a Kaizen Practitioner Certification Course teach you?
- Principles of Kaizen and continuous improvement.
- Practical tools and techniques for identifying and solving problems.
- Implementing Kaizen events and sustaining improvements over time.
Who should take Kaizen Practitioner Certification course?
- Professionals in manufacturing, operations, and quality control roles.
- Individuals seeking to enhance their problem-solving and continuous improvement skills.
- Those involved in process improvement and lean initiatives.
Why should take Kaizen Practitioner Certification course?
- To gain practical skills in implementing continuous improvement initiatives.
- To improve efficiency, reduce waste, and enhance quality within the organisation.
- To foster a culture of continuous improvement and employee engagement.
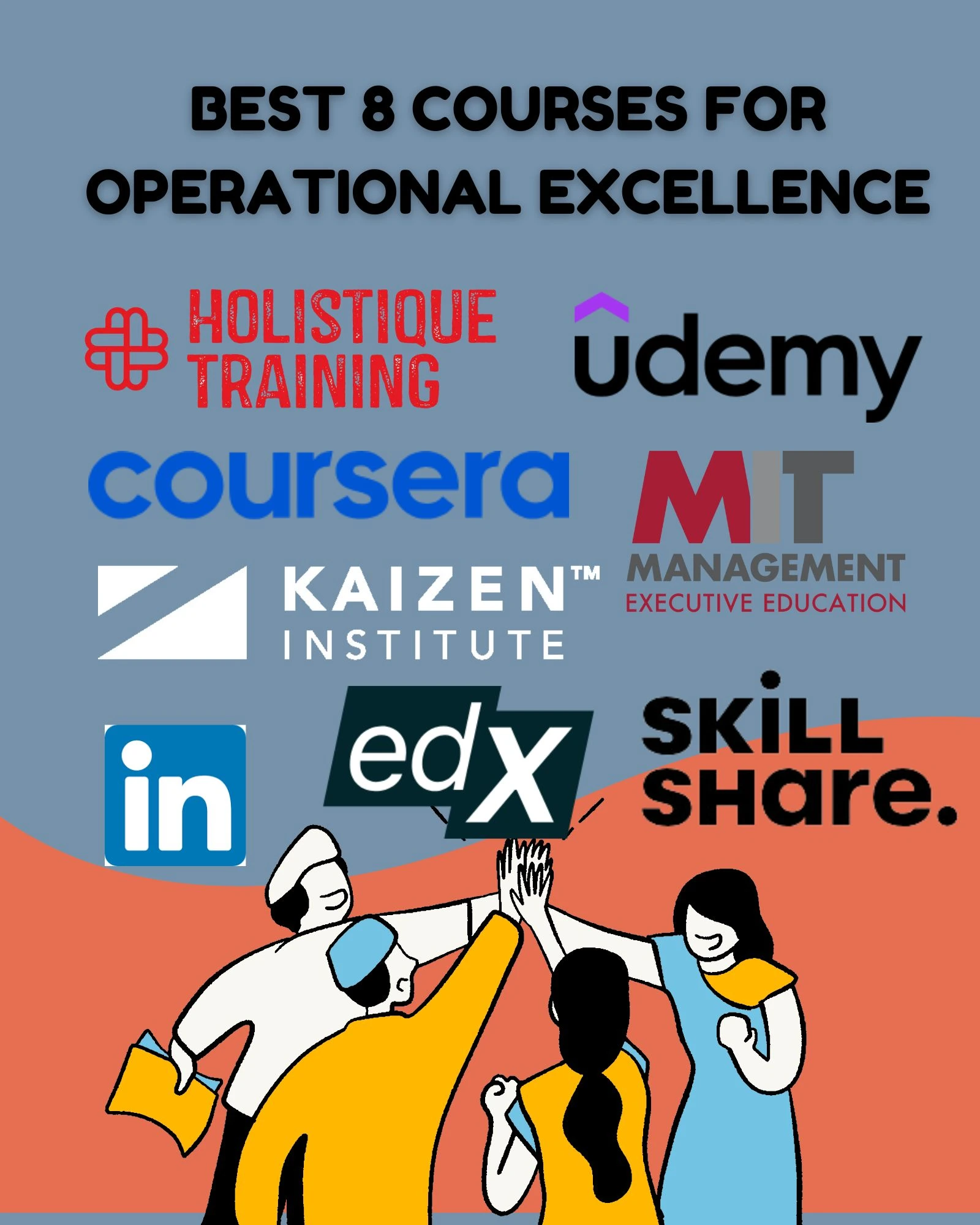
4. Total Productive Maintenance (TPM) Certification (Udemy)
- Summary: This course covers the Total Productive Maintenance (TPM) methodology, aiming to maximize equipment effectiveness and minimise downtime. Participants learn maintenance best practices and improvement techniques.
- Duration: 2 weeks
- Language: English
- Level: Intermediate
What does a Total Productive Maintenance (TPM) Certification Course teach you?
- Principles and practices of Total Productive Maintenance.
- Techniques for preventive maintenance, equipment management, and reliability improvement.
- Implementing TPM programs and improving overall equipment effectiveness.
Who should take the Total Productive Maintenance (TPM) Certification course?
- Maintenance professionals, engineers, and managers.
- Individuals responsible for equipment management and reliability improvement.
- Those seeking to enhance their skills in maintenance and operational efficiency.
Why should take Total Productive Maintenance (TPM) Certification course?
- To improve equipment reliability and reduce downtime.
- To enhance maintenance practices and increase operational efficiency.
- To contribute to the overall productivity and effectiveness of the organisation.
5. Business Process Management (BPM) Certification (edX)
- Summary: This course focuses on Business Process Management (BPM) principles and practices. Participants learn to analyse, design, implement, and monitor business processes to achieve operational excellence.
- Duration: 1 week
- Language: English
- Level: Intermediate
What does a Business Process Management (BPM) Certification Course teach you?
- Fundamentals of BPM and process improvement.
- Techniques for process mapping, analysis, and redesign.
- Implementing and monitoring BPM initiatives for continuous improvement.
Who should take Business Process Management (BPM) Certification course?
- Business analysts, process managers, and operations professionals.
- Individuals involved in process improvement and organisational development.
- Those seeking to enhance their skills in BPM and operational efficiency.
Why should take Business Process Management (BPM) Certification course?
- To improve business processes and achieve operational excellence.
- To enhance skills in process analysis, design, and implementation.
- To contribute to the overall efficiency and effectiveness of the organisation.
6. Operational Excellence in Manufacturing (LinkedIn Learning)
- Summary: This course provides an in-depth understanding of operational excellence in manufacturing settings, focusing on lean principles, waste reduction, and process optimisation.
- Duration: 2 weeks
- Language: English
- Level: Intermediate
What does an Operational Excellence in Manufacturing Course teach you?
- Lean manufacturing principles and waste reduction techniques.
- Process optimisation and efficiency improvement strategies.
- Tools for identifying and eliminating bottlenecks in production processes.
Who should take Operational Excellence in Manufacturing course?
- Manufacturing professionals, engineers, and managers.
- Individuals involved in process improvement and lean manufacturing initiatives.
- Those seeking to enhance their skills in manufacturing efficiency and quality control.
Why should take Operational Excellence in Manufacturing course?
- To gain practical skills in lean manufacturing and process optimisation.
- To improve efficiency and reduce waste in production processes.
- To contribute to the overall productivity and quality of manufacturing operations.
7. Continuous Improvement: Tools and Techniques (Skillshare)
- Summary: This course focuses on various tools and techniques for continuous improvement, providing participants with practical skills to drive operational excellence in their organisations.
- Duration: 1 week
- Language: English
- Level: Beginner to Intermediate
What does a Continuous Improvement: Tools and Techniques Course teach you?
- Various continuous improvement tools and techniques.
- Methods for identifying and solving operational problems.
- Strategies for sustaining improvements and fostering a culture of excellence.
Who should take Continuous Improvement: Tools and Techniques course?
- Professionals across various industries involved in process improvement.
- Individuals seeking to enhance their problem-solving and continuous improvement skills.
- Those looking to implement continuous improvement initiatives in their organisations.
Why should take Continuous Improvement: Tools and Techniques course?
- To gain practical skills in continuous improvement methods.
- To improve operational efficiency and effectiveness.
- To foster a culture of continuous improvement and excellence within the organisation.
8. Developing Operational Excellence In The Process Industry (Holistique Training)
- Summary: Operational excellence courses teach best practices for improving efficiency, identifying and addressing technical and human risks, and developing customised improvement plans. Participants learn to apply benchmarking techniques, leverage High-Reliability Organisations (HROs) experiences, and design effective action plans to foster a culture of operational excellence across the organisation.
- Duration: 5 days
- Language: English
- Level: Intermediate to Advanced
What does a Developing Operational Excellence In The Process Industry Course teach you?
- Best practices for achieving operational excellence.
- Identifying and outlining the effects of technical and human risks on operations.
- Developing customised operational improvement plans that address significant risks.
- Applying benchmarking techniques to generate performance metrics.
- Leveraging the experiences of High-Reliability Organisations (HROs).
- Designing effective action plans to inculcate operational excellence across the organisation.
Who should take Developing Operational Excellence In The Process Industry course?
- Professionals in the process industry seeking to improve operational efficiency and effectiveness.
- Managers and leaders responsible for overseeing operations and implementing improvement initiatives.
- Individuals involved in risk management, process improvement, and quality control within the process industry.
Why should take Developing Operational Excellence In The Process Industry course?
- To gain a comprehensive understanding of the process industry's best practices for operational excellence.
- To learn how to identify and mitigate technical and human risks that impact operations.
- To develop skills in creating and implementing customised improvement plans and performance metrics.
- To leverage insights from High-Reliability Organisations to enhance operational practices.
- To design and execute action plans that foster a culture of operational excellence within your organisation.
Course Name | Platform | Duration | Language | Level |
Lean Six Sigma Green Belt Training | Coursera | 4 weeks | English | Intermediate |
Operational Excellence for Leaders | MIT Sloan Executive Education | 1 week | English | Advanced |
Kaizen Practitioner Certification | Kaizen Institute | 1-2 weeks | English | Intermediate |
Total Productive Maintenance (TPM) Certification | Udemy | 2 weeks | English | Intermediate |
Business Process Management (BPM) Certification | edX | 1 week | English | Intermediate |
Operational Excellence in Manufacturing | LinkedIn Learning | 2 weeks | English | Intermediate |
Continuous Improvement: Tools and Techniques | Skillshare | 1 week | English | Beginner to Intermediate |
Developing Operational Excellence In The Process Industry | Holistique Training | 5 days | English | Intermediate to Advanced |
Table: Summary of Best 8 Courses for Operational Excellence
Conclusion
Achieving operational excellence is vital for organisations striving to enhance efficiency, reduce waste, and create sustainable value. The eight courses highlighted in this article provide diverse pathways to mastering key principles, methodologies, and operational excellence practices. Whether you are a leader aiming to foster a culture of continuous improvement, a professional seeking to refine your technical skills, or an organisation looking to enhance overall performance, these courses cater to various levels and industries.
Choose the course that best aligns with your career goals and operational needs, and take the first step toward building a culture of excellence in your organisation.